
Services
ESSINOX, a company at your service.
Anxious to meet the requirements of our customers, we offer a diversity of services to simplify and certify the best quality for all our products.
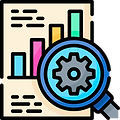
Research & Development
SALVI valves
The SALVI valves R&D department is dedicated to the innovation and design of valves and accessories.
We also work with our customers to develop tailor-made solutions to meet their specific needs.
Our goal is to offer high quality faucet products that meet the highest standards for performance, energy efficiency, durability, reliability and safety.
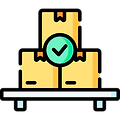
Stock
Piping:
Essinox offers a wide range of so-called “classified” nuclear products for nuclear power plants: stainless and non-alloy steel tubes, seamless and welded, BW and SW fittings, flanges, and rolled and forged bars.
These various products are manufactured and stored mainly according to the RCC-M code but also according to other codes such as RCC-Mx, RCC-MRx.
The same type of products is available and qualified according to the ORANO Standards (COGEMA) for fuel reprocessing plants.
SALVI valves:
SALVI valves have a wide selection of standard valves in stock.
In addition, thanks to an optimized stock of spare parts, we can respond to certain urgent requests.
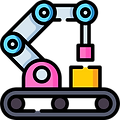
Machining and subcontracting
Piping:
On request, we can cut our long products (tubes, bars) to meet precise lengths. Generally, we do not detail our tubes (except in very exceptional cases) unlike the bars that we use for cutting.
Our machining centers allow us not only to manufacture our own fittings but also to offer our customers, consumers of raw materials, the opportunity to machine their parts according to their plans.
SALVI valves:
The machining carried out internally or externally is defined by our plans and according to standards.
Our subcontractors deliver us compliant controlled parts on which we carry out checks; either by sampling; or 100% depending on the projects.
All of our suppliers are qualified, monitored and audited regularly to ensure the quality standards of our products.

Mechanical transformation / Factories
Piping:
In order to offer a complete range, Essinox offers different types of fittings in addition to tubes. These fittings allow, among other things, changes of direction (elbows, bends), diversions (tees, bosses), changes in diameter (reductions), connections of two circuits or tubes (flanges, union fittings, sleeves), circuit closures (caps, plugs) …
For seamless tubes , mechanical transformation actions are carried out in the factory. Depending on the diameters and the tools used by the factories, we will talk about mandling, rolling, extrusion or drawing.
For fittings , there are two main families:
“ Butt Welding ” fittings symbolized by BW and “Socket Welding” fittings symbolized by SW.
Just as with its seamless tubes, basic products for the production of its BW fittings, Essinox entrusts its manufacturing to its partner factories and we will then talk about bending, hydraulic forming and stamping (caps).
For SW fittings, Essinox transforms its forged bars and blanks (elbows and tees) with its own machining means.

Destructive controls
Piping:
Essinox has chosen to entrust all destructive tests to independent laboratories which have COFRAC accreditation (ISO 17025).
We thus guarantee our customers the transparency, impartiality, reliability and accuracy of the results of our retests.
In the same way as for our internal achievements, all our customers can follow the precise steps carried out in our partner laboratories.
Below you will find a non-exhaustive list of the tests carried out:
Chemical analysis :
Chemical analysis by SEO: C Si Mn SP Ni Cr Mo Cu Ti Nb Co V Al B
Chemical analysis Nitrogen by reductive fusion
Mechanical Tests:
Traction on cylindrical or prismatic specimen at ambient temperature according to NF EN ISO 6892-1/16
Traction on cylindrical or prismatic specimen at T° > 200°C and < 700°C according to NF
EN ISO 6892-2/18
Flattening test according to NF EN ISO 8492/04
Flaring test according to NF EN ISO 8493/04
Bending test NF EN ISO 7438/18
Bending test by impact from 0°C to -196° according to NF EN ISO 148-/17
Corrosion tests:
According to SGN Pr M021 Ind F standard with microphone, on internal or external skin
According to RCC-M
According to MONYPENNY STRAUSS NF EN ISO 3651-2/98
Micrographic Examination:
According to SGN and RCC-M standards
Determination of grain size index with photos.
Ferrite rate by micrograph (ASTM E562)
Ferrite rate by micrograph (ISO /TC17/SC7 n) 306F, NF A05-165)
Content of inclusions (ASTM, NF EN)
Ferrite rate by ferritescope
Depending on the projects, we can carry out additional checks upon receipt of the raw material or processing.

Supply
Piping:
As part of our stockist activity, we constantly monitor the correct levels of our stocks. We guarantee our customers the availability of products manufactured according to the RCC-M code. According to the qualitative requirements of the RCC-M, each product manufactured and stored has full traceability (from the steelworks to the final product), and is subject to the surveillance of EDF DI (formerly EDF CEIDRE) throughout its production until 'to being put into stock in our racks.
All our supply specifications are validated by EDF UTO, so the release of RCC-M equipment from stock is simplified for our customers since the equipment manufactured has been checked and validated by EDF upstream and is ready for assembly.
Systematically, when we process a supply for a customer, we submit quality plans which allow them to follow all stages of manufacturing.
Note that we meet the requirements of the RCC-M F6000 with a storage area II.
SALVI valves:
Raw materials are supplied according to EN, ASME or RCC-M standards depending on customer needs. The characteristics and traceability are defined in our internal procedures of our ISO 9001/19443 quality system and carried out from supply to receipt.
Material certificates are submitted to clients, depending on the projects, for validation in our Internal Quality Monitoring Documents (DSI).
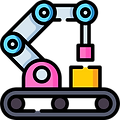
Special and personalized markings
SALVI piping and valves:
Basic and to meet traceability requirements, all our materials are marked. We systematically find the casting and batch numbers, the grade, the manufacturing standard or code, the manufacturer and the specific dimension of the product.
All our marking systems are adapted to the products and code/standard constraints. We find the following means: ink markings, electrolytic, percussive and vibrating engraving, laser (when authorized) and for temporary, metal writings and other markers.
All marker-type inks and application markings are PMUC (Products and Materials Usable in Central Plant).
Essinox goes even further and offers its customers specific markings: adding color codes, Item numbers, bar codes... the only limit will be the size of the support.

Chemical / Thermal Treatment
Piping:
Systematically, all our stock products have been pickled and passivated according to RCC-M F6000, these are chemical surface treatments in the same way as degreasing, nitriding, phosphating, etc.
To respond to various emergencies, Essinox can carry out stripping/passivation on small parts in its workshops.
However, for special manufacturing, we call on specialist service providers.
Essinox can also manage heat treatments to obtain specific mechanical and structural properties of certain steels (case-hardening or structurally hardening steels) or simply to standardize non-alloy steel.
SALVI valves:
Depending on the projects, we are required to carry out specific treatments such as painting, stripping/passivation, etc. We use qualified service providers.

Certificates – End of Manufacturing Report (RFF)
SALVI piping & valves:
At the end of the manufacturing of equipment, an End of Manufacturing Report (RFF) is established: this document is composed at least of a quality plan (PQ), material certificates 3.1 and associated minutes.
The PQ details all the stages of manufacturing the equipment with the name of the operator, the applicable documents for carrying out the operation, and the associated minutes in order to ensure complete traceability.
Other documents such as the Instructions covering the topics of use, installation and maintenance can be provided.
Each report is established, verified and approved by the quality department.
ESSINOX will move to the digitalization of its processes and documentation in 2024 in partnership with Siteflow.
Thanks to this new solution, no more paper! Paper instructions and minutes are replaced by tablets in the workshop, which allows operators to report information on product manufacturing in real time.
All information entered on the tablets (signatures, minutes, etc.) is automatically sent to the software. The RFFs are then automatically generated by the quality department, which saves time on drafting the RFFs, makes the data more reliable (no more duplicate entries/copying errors), and provides precise and specific instructions for the various manufacturing operations for operators.
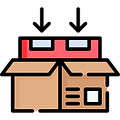
Special and personalized packaging
Packaging is an important step in our distribution processes because it guarantees the integrity of the products during transport.
Piping:
Systematically, our RCC-M stainless steel tubes are fitted with caps, protected by PMUC sheaths and our fittings are in individual packaging.
We are able to meet the requirements of each of our customers, such as:
-
When our customers ask us for boxes, we use at least wood treated to the NIMP15 standard and when these boxes must be transported by boat we follow the SEI4C standard.
-
For EDF UTO we provide “long-lasting” packaging (5 years) meeting CSCT 43922618
SALVI valves:
After the cleaning procedure, we proceed to packaging the equipment, adapting our methods to the codes and standards governing each client's activity. We also offer the possibility of creating tailor-made and personalized packaging, in order to precisely meet particular requirements.

Shipping
SALVI piping and valves:
To ensure our deliveries, we use various channels depending on the type of products transported but also according to the degree of urgency.
Classically, we charter heavy goods vehicles for long, bulky or heavy products and use postal courier such as UPS/TNT for small parts.
In emergency cases, we use so-called “taxi” carriers making direct deliveries with certainty of delivery times.
In all cases, we avoid shortages, we ensure our customers' means of unloading and adapt the vehicles accordingly.
All of our partners' drivers are authorized to deliver to central locations.
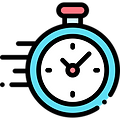
Adapted and fast deadlines
Piping:
Essinox is called upon daily on various unit outages across the national territory and resorts to urgent manufacturing or stock releases.
Also, we control ultra-short deadlines in the same way that we manage deliveries scheduled over several years.
Whatever the supply problem for your construction sites, Essinox will be available to support you.
SALVI valves:
We can respond to your emergencies and consult us.

Assemblies
SALVI valves:
The assembly and assembly of our equipment is carried out in our workshop by trained and qualified personnel.
Marking (laser, micro-percussion, electrolytic, etc.) and cleaning of parts (Ultrasonic tank, acetone, etc.) are an integral part of the manufacturing process.
The assembly, marking and cleaning procedures are written, reviewed and validated by the technical services as well as the quality department.
These procedures are listed in our quality system.
In addition, a monitoring file can be produced to follow each stage of manufacturing and impose stop points or convening points at the customer's request.
Once manufacturing is completed, a complete review of the tracking file or the manufacturing order is carried out by the quality department before shipping the material.
Conditioning and packaging according to our procedures helps protect all equipment. Special requirements can be made at the customer's request.

Non-destructive testing
Non-destructive testing is used to characterise the structural integrity of materials, without damaging them.
-
Ultrasonic testing and thickness measurement
Piping :
Almost all the materials in our stock have undergone ultrasonic testing. This method allows us to detect imperfections of various sizes in the material and thus to rule out non-compliant materials.
One of Essinox's strengths is that it has a very large number of tube standards (for checking tubes) and step gauges (for sheet metal), as well as having designed its own semi-automatic checking bench for tubes.
Essinox uses a COFREND level 2 operator for inspections and a COFREND level 3 operator to validate its specifications.
-
Penetrant testing
Essinox réalise ses ressuages dans sa salle dédiée de l’atelier avec son personnel qualifié COFREND.
Piping & SALVI Valves:
This inspection method reveals surface defects or defects emerging on the surface of a metal, classified into two categories (linear or rounded).
Depending on the project, we can carry out additional checks as soon as the raw material or machining is received.
Penetrant testing is carried out by COFREND level 2-certified in-house personnel. Chemical analyses, mechanical or corrosion tests, or any other specific requests are entrusted to qualified independent partner laboratories with COFRAC accreditation (ISO 17025).
-
Endoscopy
Piping
For more detailed visual inspection, Essinox has a powerful endoscope that can be used to inspect the inside of pipes, as well as specific parts where direct vision is no longer sufficient (e.g. pocket with deep borehole).
Our equipment enables inspections to be carried out over lengths of more than 8 m, in holes with a diameter of at least 6 mm. We can also record videos and photos.
A defect characterisation booklet and standards ensure that inspections are correctly interpreted.
This method of indirect visual inspection adds to the wide range of services available in-house, and our staff are COFREND-qualified.
-
Hydraulic tests
Pressure tests on our equipment are carried out in accordance with EN, ASME or RCC-M standards
Piping :
Thanks to its R&D department, Essinox has developed tools to carry out hydraulic tests and trials in small and medium series, on flanges, SW and BW fittings (Ø<= 4''), tubes, and any other parts on study.
Our specifications have been approved by FRAMATOME and EDF, and our staff are qualified to perform these tasks.
SALVI Valves:
Hydraulic tests on our equipment are carried out in our workshop in compliance with standards NF EN 12266-1, NF EN 12266-2 and CST 45 C 015 or special requirements:
Casing strength (hydrostatic test) Test P10
Casing tightness Test P11
Seat tightness Test P12
Obturator strength Test P20
Manoeuvrability Test F20 following
Inspections, tests or reports can be supplied at the customer's request, depending on the project.
-
Visual and dimensional checks
Piping and SALVI Valves :
In order to check our stock parts and those specially manufactured for our customers, we have a very wide range of checking equipment enabling us to draw up our CVD reports (Visual and Dimensional Checks). This equipment, which is constantly kept up to date with calibration, includes callipers, gauges, measuring columns, protractors, threading pads and rings, etc.
This wide range of equipment is complemented by a WENZEL Smart CMM three-dimensional measuring machine, which combines intelligent technology with high measurement performance. It enables parts and components to be inspected more quickly, with greater precision.
All our operators with a valid visual acuity certificate are authorised to use these instruments.
-
Radio controls
Piping :
In the process of manufacturing welded tubes, we check the welds by radioscopy.
In order to comply with radiation protection standards, the operations are carried out on our premises, usually at the end of the day or at night, under the supervision of our authorised partners. The films are then interpreted and stored in a controlled atmosphere in-house.